El cross docking o traspaso de mercancías de muelle a muelle, supone en sí mismo una mayor agilidad del flujo de mercancías dentro de nuestro almacén. No solo a nivel distribución también de producción, pensemos que el muelle de destino puede ser el de un WIP¿? (aunque sea un muelle virtual).
“El almacén más rentable, es aquél que no existe”
Y el cross docking se acerca mucho a esta afirmación desde varios frentes. No es que el cross docking en sí mismo mejore otros procesos, es que o bien directamente se los salta por innecesarios o reduce su tiempo de proceso dado que sólo ejecutaremos la parte del proceso estrictamente necesaria. Esto va a suponer un ahorro de almacenaje, de manipulación, de recursos y financiero.
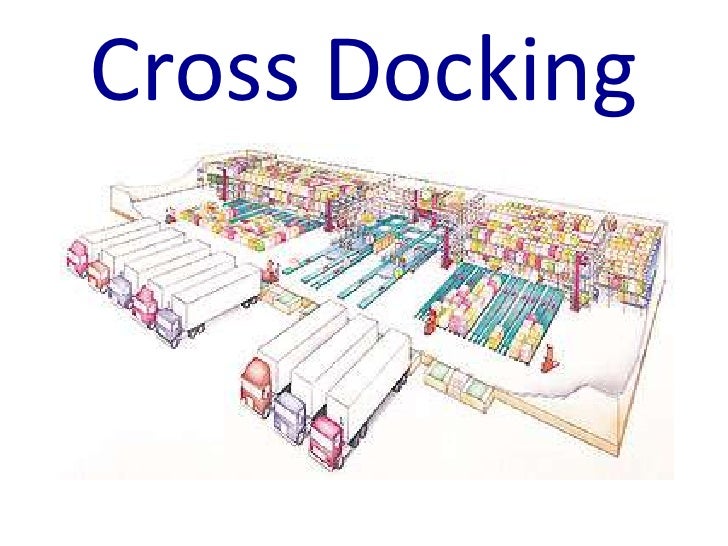
En el cuadro podemos ver la diferencia que existe entre un almacén que no cuenta con una gestión en la que se incluya el cross docking y otro en el que sí.
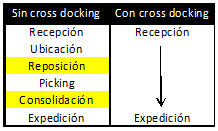
En el cuadro vemos el caso más favorable de cross docking directo, es decir, aquél que no necesita manipulación por nuestra parte porque las unidades de embalaje a expedir son las mismas que se han recibido y que como mucho habría que redistribuir en diferentes muelles.
La diferencia de procesos que intervienen en la consecución del mismo objetivo (que es la expedición) es notable y esto redunda siempre en beneficio. Hemos resaltado en amarillo dos procesos porque dependiendo del tipo de referencia y almacén pueden darse o no en un almacén sin cross docking. En el caso de que nuestro cross docking no pueda ser directo, es decir, que requiera cierta manipulación y consolidación.
El cross docking aumenta la velocidad del flujo de materiales para servir, reduce los costos y riesgos de manipulación y desde luego reduce los costos de almacenamiento.
Descarga gratis el Caso de Éxito de SGA:
Cómo conseguir ahorros de hasta 40% en costes de expedición
Si a todo ese ahorro en procesos añadimos la negociación con nuestros proveedores, para que las unidades logísticas de distribución sean exactamente las que nuestro cliente necesita (sea interno o externo), tenemos a nuestra disposición una ventaja estratégica que aún nos ahorrará recursos y riesgos propios de la manipulación, que ese caso sería la mínima imprescindible. Todo esto siempre acaba convirtiéndose a efectos prácticos en mejoras notables de la productividad de cada proceso interviniente y de nuestro almacén en general.
Ejemplo real:
Veámoslo con un ejemplo real. Situémonos en un almacén que suministra materia prima y producto terminado a sus propias cadenas de producción y montaje. Además debe expedir contenedores de producto semielaborado a proveedores externos para que realicen ciertos procesos y recibirlos una vez han sido procesados. Estos semielaborados serán enviados también a su propia cadena de producción. Por supuesto nuestro almacén cuenta con varios muelles de entrada y de salida en zonas diferenciadas.
Tenemos los muelles a rebosar de contenedores de piezas y palés llenos de cajas que debemos distribuir rápidamente a diferentes clientes internos y externos. Ni siquiera vamos a describir lo que esto supondría para un almacén sin SGA, sería prácticamente misión imposible, pero para un almacén con un SGA que NO dispusiera de la posibilidad de hacer cross docking, supondría que después de dar entrada a todos los palés y contenedores, habría que ubicarlos y hasta que no estuvieran ubicados no empezarían a activarse las llamadas desde los distintos centros de producción y trabajo que necesiten estas referencias. Esto obligaría además a hacer un picking de las referencias y distribuirlas a sus diferentes destinos. En los casos en que la necesidad cubriera el 100% de la cantidad recibida, estaríamos haciendo un 100% de movimientos de ubicación y picking completamente innecesarios. Incluso podría darse el caso de que el SGA nos obligara a reponer antes de dar paso a las órdenes de picking.
Si hablamos de un palé o un contenedor, la diferencia no es tan notable pero imaginemos que en el caso expuesto tengamos treinta o cuarenta contenedores y/o palés por entrada. La experiencia nos ha revelado que en los casos en que ocurre esto, directamente se trampea el sistema. Se crean ubicaciones falsas para llevar virtualmente allí la mercancía y se fuerza al sistema para que lance lo antes posible órdenes de picking contras dichas ubicaciones falsas. Luego las ubicaciones del material restante se hacen por traspasos manuales… en fin. Tener un sistema de gestión y al mismo tiempo, tener necesidad de trampearlo es un indicativo de las ineficiencias del propio sistema. Además siempre acaba trayendo problemas de otra índole, las trampas quizá “apaguen el fuego de hoy” pero dejan ascuas que encenderán otro (peor) mañana.
La diferencia de gestión del mismo caso anterior pero en un almacén asistido con un SGA con capacidad de hacer cross docking, como es el de DATADEC, es bien notable. El cross docking en un SGA debe ser un proceso que se ejecute cada “n” segundos (siendo “n” configurable por el usuario en el que chequea las zonas con stock disponible que acabemos de recibir y verá las necesidades de los diferentes destinatarios internos o externos. Estas necesidades pueden venir determinadas por fecha de entrega, por falta de stock, por falta de suministro, pedidos pendientes, etc. Hecho esto, lanzará las órdenes de almacén a los diferentes operarios, indicará a cada operario dónde acudir, qué mercancía trasladar, la cantidad exacta y el destino (sin almacenar, sino directamente a destino final) y esperará la captura de información que garantice que el movimiento es correcto.
Si hubiera más cantidad de referencias que necesidad, a continuación el SGA cursa las órdenes de a los operarios, de forma automática, para que lleven la mercancía a las ubicaciones asesoradas por el SGA a la zona de almacenaje.
Supongamos ahora por ejemplo que nuestro departamento de calidad, bloquea ciertos palés o ciertas referencias total o parcialmente. No importa, el SGA realizará un cross docking en diferido, es decir, será capaz de lanzar las órdenes de almacén necesarias para la distribución de estas referencias sólo cuando éstas se hayan desbloqueado y hayan pasado a estado A de Aceptación.
No hay comentarios:
Publicar un comentario